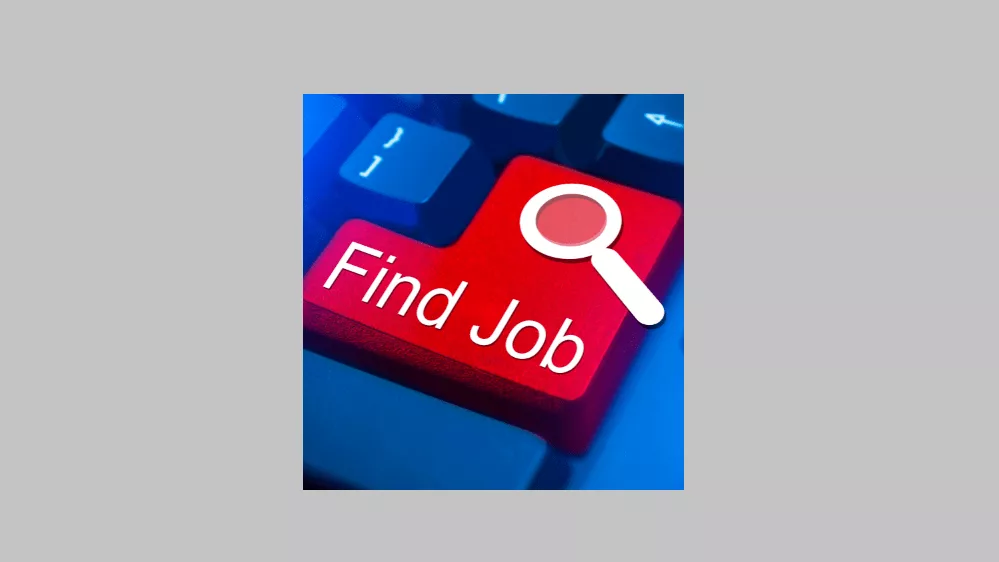
Summary: Works in production to achieve targeted results in safety, product quality, and output.
Summary: Works in production to achieve targeted results in safety, product quality, and output.
Responsibilities: Other duties may be assigned.
General:
1. Ability to operate department equipment: Stretcher, Saws, Blaster, Sander Furnace, Pickling Area, Bump Presses, and Inspection, in a safe and efficient manner.
2. Participates in Continuous Improvement activities and maintains Plymouth Tube Housekeeping Standards.
3. Reviews/records component data, when needed.
4. Ability to execute the production plan to ensure on time delivery to our customers.
5. Updates Value Stream Leader and or department LPM on employee, quality, production and safety issues.
6. Inspects and inventories site-generated hazardous waste staging areas.
7. Assists the transfer of site-generated hazardous waste to on-site staging areas.
8. Directs storage of site-generated hazardous waste in the hazardous waste staging areas.
9. Conducts inspections of Satellite Accumulation Areas.
10. Own and role model Plymouth Tube values and behaviors by embracing and participating in an operating culture that promotes involvement, communication, mutual trust & respect, expectations and accountability, and a passion for excellence.
11. Understands, applies and advocates all Company Environmental and Safety policies, procedures and standards.
12. Understands, applies and advocates all Company Quality Standards.
13. Attends all prerequisite training as required by management.
14. Has the authority to stop process to correct quality, safety or environmental problems, and to promptly notify Supervisory personnel when processes are noncompliant
Material Handler (not all Process Managers are required to learn this skill block):
1. Organizes and stages finished product for scheduled loading and shipping.
2. Accurately completes shipping paperwork and assists in data entry of shipping information.
3. Loads and unloads trucks.
Water Spider (not all Process Managers are required to learn this skill block):
1. Solid understanding of workflow and value streams
2. Moves bundles to designated areas.
3. Moves material on and off stretchers and blasters
4. Informs LPMs and VSLs of potential production issues, flow/product
5. Assists with setups
6. Assists with training at Stretchers and Blasters.
7. Maintains visual scheduling boards
8. Looks at scheduling to ensure downtime accounted for at the stretchers and blasters.
9. Reviews press schedule to determine space needs and notify LPMs and VSLs of issues.
10. Assists with sampling and resampling through area.
11. Notifies scheduling of rework needs.
Competencies:
1. Must be self-motivated and able to work without direct supervision.
2. Receptive to new and different ideas
Supervisory Responsibilities: Not applicable
Qualifications: To perform this job successfully, an individual must be able to perform each essential duty satisfactorily. The requirements listed below are representative of the knowledge, skill, and/or ability required. Reasonable accommodations may be made to enable individuals with disabilities to perform the essential functions.
Education and/or Experience: High School Diploma or GED. Previous manufacturing experience is preferred.
Certificates/Licenses/Registration: Powered Industrial Equipment Certification
Technology and Equipment: To perform this job successfully, an individual must have a working knowledge of:
1. Windows operating systems & programs
2. Microsoft Office Suite
3. Ability to use calipers
Language Skills:
To perform this job successfully, an individual should possess the following language skills:
1. Can speak and communicate effectively to technical and non-technical team members.
2. Can correctly interpret documents such as written instructions, spreadsheets, drawings, lists and manuals.
Mathematical Skills:
Demonstrate ability to add, subtract, multiply, and divide in all units of measure, using whole numbers, decimals, negative and positive numbers. Demonstrate ability to compute rate, ratio, and percent and to interpret bar graphs & use the Metric System.
Physical Demands: See Finish Medical Standards Matrix
Work Environment: The work environment characteristics described here are representative of those an employee encounters while performing the essential functions of this job. Reasonable accommodations may be made to enable individuals with disabilities to perform the essential functions.
While performing the duties of this Job, the employee is regularly exposed to moving mechanical parts, heavy equipment and stored energy in the form of pneumatic, hydraulic, mechanical, electrical and gravitational energy. The noise level in the work environment is above 85 dcB and hearing protection is required. Due to manufacturing technologies utilized in the area common contaminants such as dirt, dust, grease, oil steel chips and water will be present. The employee is frequently exposed to wet and/or humid conditions; extreme cold and extreme heat. Also may be exposed to fumes or dust.
*Work Environment – Special Considerations*
Please Note: This position involves working in close proximity on a regular basis to elevated magnetic fields, during performance of essential functions. These elevated magnetic fields are associated with certain equipment, including Billet Heaters and Stretchers. These magnetic field strengths exceed safe thresholds for pacemaker and implanted defibrillator (ICD) medical devices, and may cause serious device malfunction.
For personal safety purposes, persons with such personal medical devices may be precluded from this position. Evaluation of individual job placement, where applicable is conducted by management with assistance of designated medical advisors.
EOE
HOW TO APPLY
http://www.plymouth.com/careers – Search Hopkinsville
or go to www.Indeed.com